Due to the growth and improved compliance aspects of the plants operation, realization of the designed electrical system expansion capability has been met and in some cases exceeded. This now necessitating the need for renewal of aged assets. Renewal of aged and under capacity assets will enable continued reliable operation and foreseeable expansion of the plant.
Electrical load studies and risk assessments have been completed on the ETP 62HA HV Switchboard, which is the ‘hub’ of the sites High Voltage distribution network, to assess energy load growth, increasing age, and operational safety and reliability. These studies found that there were high risks associated with these assets meeting and sustaining required levels of service and recommended the replacement of the ETP 62HA HV Switchboard.
Scope of Work
Civil
- 62HA Switchroom
- Construction of new 62HA Switchroom
- Installation of new Transformer bay and firewall for new switchroom
- Conduit connections to ETP Powerstation and Galleries
- Conduit
- Installation of conduits connecting new and old electrical assets
- New assets
- Construction of structural supports for PFC
Electrical
- 62HA Switchroom
- Installation of 62HA Switchboard
- Installation of Transformer in new Transformer bay
- Redundant Assets
- Decommission and removal of redunant cables and transformers.
- Installation of HV and LV cables to replace old assets
- Installation of 62M Unit Substation to replace redundant assets removed.
- Commissioning
- Commission new assets to enable redundancy in the ETP power grid.
Innovation & Complexity
A 3D model was developed of the existing plant infrastructure from survey data, as-built drawings and site inspections to accurately incorporate the model of the new 62HA Switchroom and accompanying assets.
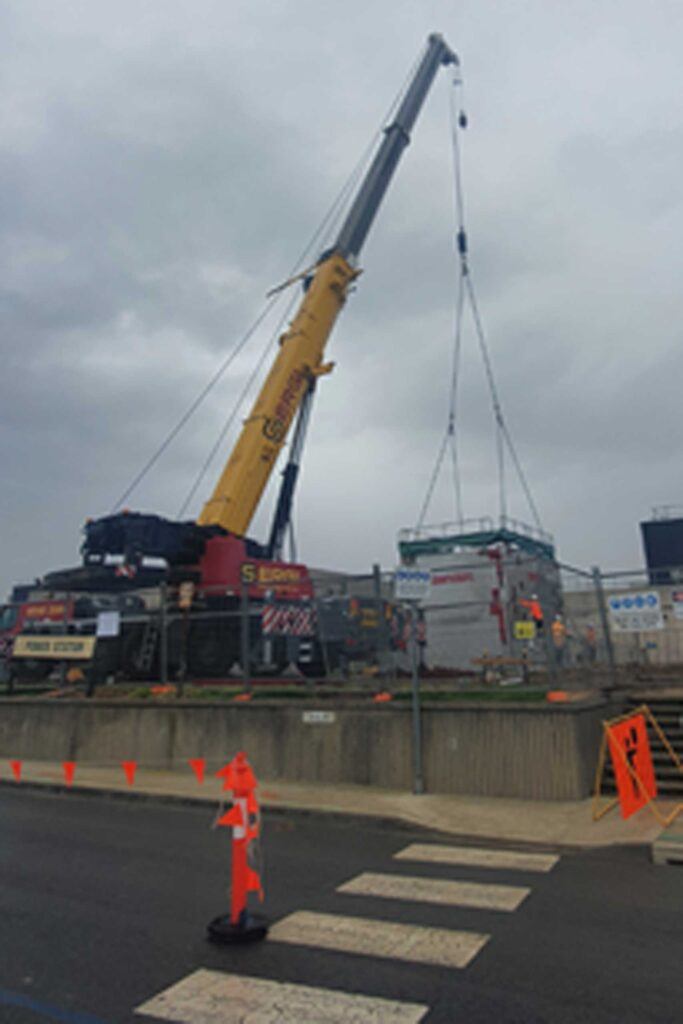
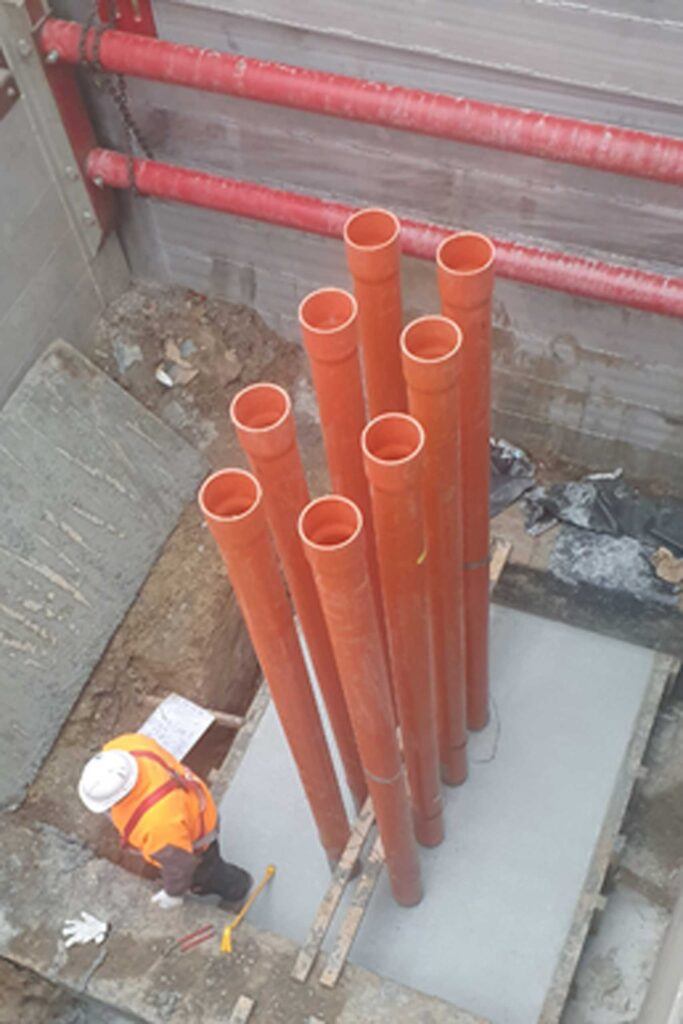
Project Outcomes
Safety
The Safety Management Plan developed at the beginning of the project defined the critical risks associated with the scope of works. Principles and procedures using the Melbourne Water Agreed Framework Safety Behaviours were developed to address and control the risks. Upon mobilisation and commencement of the project the risks were re-assessed based on the site conditions and construction methodologies to ensure all risks were addressed.
Several safety in design meetings were conducted along the design process to enable the project team to assess the methodology and deliver a constructable asset in a safe manner.
A dedicated HSEQ advisor ensured all legistlative and company procedure information was available so that the project team could ensure the safest possible environment for the construction team and any stakeholders on site.
COVID-19 presented some unique challenges for the team. Increased work space was allowed for whilst also ensuring DHHS recommendations and requirements were exceeded.
Quality
Drawing on the diverse experience of the project team, quality construction was a significant focus. All team members contributed to the variety of knowledge, maximising the product quality delivered.
Project deliverables were manufactured to engineering drawings and specifications were monitored by qualified personnel, with quality inspections and audits conducted to ensure products met the specifications.
ITPs are developed by SFP for self performing construction deliverables, and also developed by subcontractors for all manufactured / subcontractor deliverables. ITPs form the basis for review and acceptance and are reviewed by qualified SFP personnel.
Products and services identified as non-conforming were identified and reported for immediate corrective action to ensure there was no impact to the project’s schedule or cost.
Key Staff Involved
Dee Ivanovic
Project Manager
Jody Friend
Construction Manager
Eric Tann
Project Engineer
Rod Lowe
Construction Manager
Daniel Simpson
Project Engineer
Anthony Scammel
HSEQ
Adrian Williams
Site Supervisor
Y10307